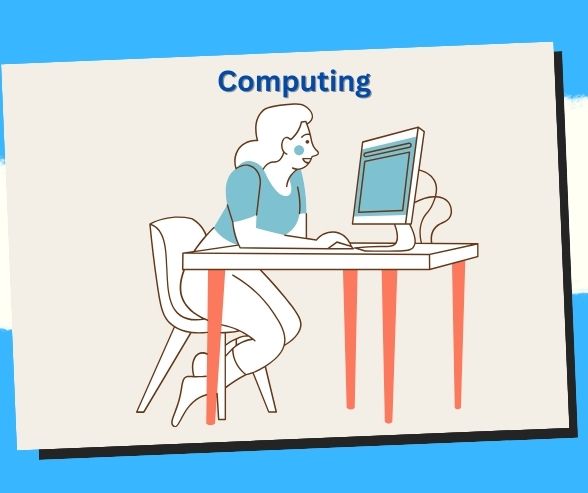
Transforming Manufacturing: Setting Up Edge Computing for Predictive Maintenance
Discover how setting up edge computing for predictive maintenance can revolutionize manufacturing processes, ensuring uninterrupted production and reduced downtime.
Mastering Predictive Maintenance with Edge Computing in Manufacturing 

In the world of manufacturing, downtime can be costly. Unplanned equipment failures can disrupt production schedules, lead to expensive repairs, and impact the bottom line. However, with the rise of edge computing, manufacturers now have a powerful tool at their disposal to implement predictive maintenance strategies, minimizing downtime and maximizing efficiency. In this comprehensive guide, we’ll explore how you can set up edge computing for predictive maintenance in manufacturing and ensure your operations run smoothly.
Understanding Edge Computing for Predictive Maintenance
What is Edge Computing?
Edge computing is a distributed computing paradigm that brings computation and data storage closer to the source of data generation. By processing data locally at the edge of the network, edge computing reduces latency, conserves bandwidth, and enables real-time insights and actions.
Why Edge Computing for Predictive Maintenance?
In the realm of manufacturing, where every minute of downtime can translate to lost revenue, predictive maintenance is crucial. By leveraging edge computing, manufacturers can analyze equipment data in real-time, detect potential issues before they escalate into failures, and schedule maintenance proactively, minimizing downtime and maximizing productivity.
Setting Up Edge Computing for Predictive Maintenance
1. Identify Critical Equipment and Sensors
Begin by identifying the critical equipment and sensors within your manufacturing facility that are key to production processes. These could include motors, pumps, conveyors, or any other machinery that is essential for operations. Install sensors on these assets to collect data on performance metrics such as temperature, vibration, and energy consumption.
2. Choose the Right Edge Computing Infrastructure
Selecting the appropriate edge computing infrastructure is crucial for success. Consider factors such as scalability, reliability, and compatibility with existing systems. Cloud-based edge computing solutions offer flexibility and scalability, while on-premises solutions provide greater control over data security and compliance.
3. Deploy Edge Devices and Gateways
Deploy edge devices and gateways near the sensors to collect and preprocess data locally. These devices act as the edge of the network, performing initial data analysis and filtering before sending relevant data to the central processing unit. Ensure these edge devices are ruggedized and capable of withstanding harsh manufacturing environments.
4. Implement Machine Learning Algorithms
Incorporate machine learning algorithms into your edge computing framework to analyze equipment data and detect patterns indicative of impending failures. Train these algorithms using historical data on equipment performance and failure modes to enable accurate predictive maintenance predictions.
5. Monitor Equipment Health in Real-Time
Utilize edge computing to monitor equipment health in real-time and detect anomalies or deviations from normal operating conditions. By analyzing data at the edge of the network, you can identify potential issues before they escalate into failures, enabling proactive maintenance interventions and minimizing downtime.
6. Integrate with Maintenance Management Systems
Integrate your edge computing solution with existing maintenance management systems to streamline workflows and facilitate proactive maintenance scheduling. Ensure seamless data exchange and interoperability between edge devices and backend systems to enable automated work order generation and scheduling.
7. Ensure Data Security and Compliance
Prioritize data security and compliance when setting up edge computing for predictive maintenance in manufacturing. Implement robust encryption protocols, access controls, and data anonymization techniques to protect sensitive equipment data and maintain compliance with regulatory requirements.
Overcoming Challenges and Considerations
Network Connectivity and Reliability
Address potential challenges related to network connectivity and reliability when deploying edge computing solutions. Ensure redundant connectivity options and backup systems are in place to mitigate the risk of downtime and ensure uninterrupted data processing.
Scalability and Flexibility
Plan for scalability and flexibility when designing your edge computing infrastructure. As your manufacturing operations grow and evolve, ensure your edge computing framework can adapt to changing demands and accommodate future expansion seamlessly.
Integration with Existing Systems
Ensure seamless integration with existing systems and data sources when setting up edge computing for predictive maintenance. Leverage APIs and middleware solutions to facilitate data exchange and interoperability between edge devices and backend maintenance management systems.
Implementing edge computing for predictive maintenance in manufacturing
It holds immense potential for businesses looking to optimize operations, minimize downtime, and maximize productivity. By leveraging real-time insights at the edge of the network, manufacturers can detect equipment issues before they escalate into failures, enabling proactive maintenance interventions and ensuring continuous operations. Embrace the power of edge computing today and revolutionize your predictive maintenance strategy for success tomorrow!
Benefits of Setting Up Edge Computing for Predictive Maintenance in Manufacturing
- Reduced Downtime: Predict and prevent equipment failures before they occur, minimizing costly downtime and production losses.
- Extended Equipment Lifespan: Proactively address maintenance needs, leading to longer-lasting machinery and reduced replacement costs.
- Optimized Resource Allocation: Allocate resources efficiently by prioritizing maintenance tasks based on real-time equipment health data.
- Improved Safety: Enhance workplace safety by identifying and addressing potential hazards before they pose a risk to workers.
- Increased Productivity: Keep production lines running smoothly with fewer unplanned interruptions, leading to higher output and profitability.
- Cost Savings: Minimize repair and replacement costs by addressing issues early, and avoiding costly breakdowns and emergency repairs.
- Enhanced Data Insights: Gain valuable insights into equipment performance and usage patterns, informing strategic decision-making and process optimization.
- Scalability: Scale your predictive maintenance program effortlessly to accommodate growing manufacturing operations and evolving needs.
- Competitive Advantage: Stay ahead of competitors by adopting innovative technologies that drive efficiency and reliability in manufacturing processes.
- Sustainability: Reduce environmental impact by optimizing resource usage and minimizing waste through predictive maintenance practices.
Case Studies: Real-Life Success Stories
- Automotive Manufacturer: By implementing edge computing for predictive maintenance, an automotive manufacturer reduced downtime by 30% and increased equipment lifespan by 20%, leading to significant cost savings and improved operational efficiency.
- Food Processing Plant: A food processing plant optimized its maintenance schedules using edge computing, resulting in a 25% reduction in unplanned downtime and a 15% increase in production output.
- Steel Mill: A steel mill enhanced workplace safety by leveraging edge computing to predict equipment failures and prevent accidents, leading to a 40% reduction in workplace injuries and improved employee morale.
- Pharmaceutical Facility: A pharmaceutical facility improved regulatory compliance and product quality by implementing edge computing for predictive maintenance, ensuring equipment reliability and uptime.
- Aerospace Manufacturer: An aerospace manufacturer optimized its maintenance processes using edge computing, resulting in a 20% reduction in maintenance costs and a 10% increase in equipment uptime.
- Electronics Assembly Plant: An electronics assembly plant increased equipment reliability and reduced repair costs by deploying edge computing solutions for predictive maintenance, improving overall operational efficiency and profitability.
- Chemical Processing Facility: A chemical processing facility minimized production disruptions and optimized resource usage by leveraging edge computing for predictive maintenance, achieving greater operational resilience and sustainability.
- Textile Factory: A textile factory improved production efficiency and reduced waste by implementing edge computing for predictive maintenance, leading to higher-quality products and increased customer satisfaction.
- Paper Mill: A paper mill optimized its maintenance schedules and reduced equipment downtime by leveraging edge computing, resulting in improved productivity and cost savings.
- Plastics Manufacturing Plant: A plastics manufacturing plant enhanced equipment reliability and reduced energy consumption by deploying edge computing solutions for predictive maintenance, achieving greater sustainability and operational efficiency.
Key Takeaways
- Assess Your Needs: Identify critical equipment and potential failure points to prioritize for predictive maintenance implementation.
- Invest in Edge Computing Infrastructure: Set up edge computing devices and sensors to collect and process real-time data from manufacturing equipment.
- Implement Predictive Analytics: Use machine learning algorithms to analyze data and predict equipment failures before they occur.
- Define Maintenance Triggers: Establish thresholds for equipment health indicators to trigger maintenance alerts and interventions.
- Integrate with Existing Systems: Ensure seamless integration with existing manufacturing systems and processes to maximize efficiency.
- Train Personnel: Provide training and support to maintenance teams to effectively utilize predictive maintenance tools and techniques.
- Monitor Performance: Continuously monitor and evaluate the performance of your predictive maintenance program to identify areas for improvement.
- Optimize Maintenance Schedules: Fine-tune maintenance schedules based on real-time data insights to maximize equipment uptime and productivity.
- Collaborate Across Departments: Involve stakeholders from maintenance, operations, and IT departments to ensure alignment and success in predictive maintenance initiatives.
- Stay Ahead of the Curve: Keep abreast of emerging technologies and best practices in predictive maintenance to maintain a competitive edge and drive continuous improvement.
FAQ
Q1: What is predictive maintenance, and how does it differ from preventive maintenance?
A1: Predictive maintenance involves using real-time data and predictive analytics to anticipate equipment failures and schedule maintenance proactively, whereas preventive maintenance is based on predefined schedules or thresholds.
Q2: How does edge computing enable predictive maintenance in manufacturing?
A2: Edge computing allows real-time data processing and analysis to occur at the source, enabling predictive maintenance algorithms to operate on the shop floor without reliance on centralized servers or cloud infrastructure.
Q3: Can predictive maintenance be applied to all types of manufacturing equipment?
A3: Yes, predictive maintenance can be applied to various types of manufacturing equipment, including machinery, robotics, conveyor systems, and more, to optimize performance and reliability.
Q4: What are the key benefits of implementing predictive maintenance in manufacturing?
A4: Key benefits include reduced downtime, extended equipment lifespan, improved safety, increased productivity, cost savings, enhanced data insights, scalability, competitive advantage, and sustainability.
Q5: How accurate are predictive maintenance algorithms?
A5: Predictive maintenance algorithms can achieve high accuracy levels by continuously learning from historical data and real-time inputs, enabling early detection of equipment anomalies and failure patterns.
Q6: What types of data are used for predictive maintenance in manufacturing?
A6: Data sources include equipment sensors, operational data, maintenance logs, historical records, and external factors such as weather conditions and supply chain disruptions.
Q7: How does predictive maintenance contribute to sustainability in manufacturing?
A7: By minimizing equipment downtime and optimizing resource usage, predictive maintenance helps reduce energy consumption, waste generation, and environmental impact in manufacturing operations.
Q8: Can edge computing solutions integrate with existing manufacturing systems and equipment?
A8: Yes, edge computing solutions can be seamlessly integrated with existing manufacturing systems and equipment, leveraging industry-standard protocols and interfaces for interoperability.
Q9: What are the long-term benefits of predictive maintenance for manufacturing?
A9: Long-term benefits include improved equipment reliability, reduced maintenance costs, enhanced operational efficiency, greater sustainability, and a competitive edge in the marketplace.
Q10: How can organizations get started with setting up edge computing for predictive maintenance in manufacturing?
A10: Organizations can start by assessing their maintenance needs, investing in edge computing infrastructure, implementing predictive analytics algorithms, training personnel, and continuously monitoring performance to drive continuous improvement.
Conclusion
With the power of edge computing and predictive maintenance at your disposal, the future of manufacturing is brighter than ever before! Embrace innovation, prioritize equipment reliability, and pave the way for a smarter, more efficient production floor.
Key Phrases
- Edge computing for predictive maintenance
- Manufacturing efficiency optimization
- Proactive maintenance strategies
- Equipment performance enhancement
- Future-proofing manufacturing
- Production reliability improvement
- Predictive maintenance solutions
- Factory operations streamlining
- Equipment failure prediction
- Edge computing applications in manufacturing
Best Hashtags
- #EdgeComputing
- #PredictiveMaintenance
- #ManufacturingEfficiency
- #ProactiveMaintenance
- #FutureOfManufacturing
- #ReliabilityImprovement
- #EquipmentPerformance
- #FactoryOperations
- #MaintenanceSolutions
- #ProductionOptimization
Save/Share this story with QR CODE
Disclaimer
This article is for informational purposes only and does not constitute endorsement of any specific technologies or methodologies and financial advice or endorsement of any specific products or services.
Need to get in touch?
Feel free to Contact NextGenDay.com for comments, suggestions, reviews, or anything else.
We appreciate your reading. Simple Ways To Say Thanks & Support Us:
1.) GIVE A TIP. Send a small donation thru Paypal
Your DONATION will be used to fund and maintain NEXTGENDAY.com
Subscribers in the Philippines can make donations to mobile number 0917 906 3081, thru GCash.
3.) BUY or SIGN UP to our AFFILIATE PARTNERS.
4.) Give this news article a THUMBS UP, and Leave a Comment (at Least Five Words).
AFFILIATE PARTNERS
World Class Nutritional Supplements - Buy Highest Quality Products, Purest Most Healthy Ingredients, Direct to your Door! Up to 90% OFF.
Join LiveGood Today - A company created to satisfy the world's most demanding leaders and entrepreneurs, with the best compensation plan today.